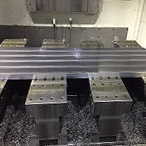
S45Cの材料
1110×339×35を
1104×333×30に加工する作業を紹介します。
段取り
治具の取り付け
治具を取り付けて平面を確認します。
一番低い所と一番高い所で0.019mmなので、荒加工後に測定をして0.019mmを拾う場合は治具を修正します。
平面の出ている治具を取り付けても平面が出るとは限りません。
治具を取り付けて、取り付けた機械で直接冶具を削った方が平面が出やすいです。
この冶具も機械で直接削った時は0に近い数値でしたが、付け外しなどで0.019mmずれています。
反りの確認
薄板材の場合材料寸法の確認の他に反りの確認が必要です。
上の写真は下図のように取り付いています。
薄板材のように反りのある材料は、下図赤丸部のように反った部分を基準面側に取り付けましょう。
今回のように反りも少なく均等に反っている場合、重量のある材料を裏返す作業はしないで、この状態で加工します。
材料を変えて、反りのある材料で少し書いていきます。
材料はSUS303の707×488×15です。
材料の仕上がり寸法11.5mm±0.1
この材料の方が薄板加工の紹介に向いているのですが、
次工程で形状に特徴が出てしまうので出来る範囲での投稿になります。
材料の厚みが15mmなので1.68mm反っています。
上の写真は、下図のように材料が傾いて反りが大きいように取り付いています。
先ほど紹介したように、反った部分を基準面側に取り付けると15.73mmと取り付ける向きで1mmの差が出ます。
加工
平面基準加工
加工方向に合わせてストッパーを付けて
端材で作った簡単バイス二か所でクランプします。
押し当てる側二か所は通りを出して取り付けて、締めるとき材料に力を加えて歪ませてしまわないように注意。
材料を固定する力が弱いので、このストッパーは位置決め用ではなく固定用に付けます。
(黒皮や形状により治具との接地面が少い場合は特に注意)
この材料は反りが少ないので黒皮がむける0.5mmで加工します。
反りの大きい材料は黒皮を残した状態で取りきれるか確認します。
取りきれない、取りきれるか怪しい場合、必ず黒皮を残した状態で報告しましょう。
大きい材料は、すを見落とさないように注意が必要です。
切削油を出して十分に冷却しながら両面黒皮がむける程度で加工します。
外周加工
簡単バイスの押し当てる側と材料の間に、外形加工に使うエンドミルの通る隙間を作るため取り付け直しします。
材料の通りだし作業を省くため、ブロックを間に入れて軽く押し当ててクランプして、
クランプ後ブロックを取り外します。
上面を加工する時の基準は、どこで取っても平気ですが
外形加工の時は中心を取って加工します。
相対座標を使って距離を測り
1231.65の半分
615.825の位置へ移動してXの絶対座標を0にします。
Yも同じく絶対座標を0にします。
Zはセンサーを使って治具で取ります。
Z0.5mmで治具に当てないように333.0を仕上げます。
同じく1104.0を仕上げます。
加工物が動かないように、クランプを一か所ずつ付け替えます。
穴加工がある場合はここで加工します。
(平面仕上げの取り代0.1mm~0.2mm深めに加工)
平面仕上げ加工
裏返して簡単バイスで取り付けます。
テスターを当てて、加工物に極端な反りが無いか上から手で押して確認し、バイスで固定するときも加工物が浮き上がらないかテスターで確認しながら固定します。
加工前の数値(加工物)、加工数値(プログラム)、加工後の数値(加工物)を確認しながら、1回で取りきれる取り代であっても加工による変形が無いか確認するため、数回の加工で慎重に仕上がり寸法の+0.3mmまで加工します。
(この記事作成後に穴加工があるので30.4仕上がりで加工します)
プログラムの加工数値と実測値に誤差がある場合ワーク座標系で調整
プログラムではZ30.7で加工しましたが実測値は30.65mmと、プログラムの加工数値よりも0.05mm多く削れているので、G54 Z軸のワーク座標に+0.05を増分入力します。
(プログラムの数値と実測値を同じにするため)
仕上げ加工になるのでフェイスミルのチップに気を使い、最初の加工面を表として測定結果に合わせて、表裏裏(1回の付け替え)、表裏表(2回の付け替え)の0.1mm×3回で仕上げます。
面粗度仕上げ作業
取り外し後の測定
寸法が30.396mm~30.410mm
面粗度がRz6.132~Rz6.996
寸法は公差に入っていますが、面粗度が公差から外れているので
RYOBIのサンダS-815Sに#80のペーパーを取り付けて仕上げ作業をします。
加工物もペーパーも最初のうちは削れやすく、だんだんと削れにくくなってくるので、加工が狭い範囲に集中しないように作業します。
サンダの加工で0.002mm~0.003mm削れたので寸法にも注意しながら加工します。
最後に
部分的に面粗度は出ていますが、機械加工に比べてムラが出るので事前に検査、設計と打ち合わせをしてから加工の選択をしましょう。
この作業で重要なのは、特定の機械でしか加工できない加工が誰にでもできる加工になる所にあります。
面粗度加工以外でも、機械の加工時間が長く加工数が多いなどで、作業者の空き時間が長くなってしまう場合、ボール盤や手作業でできる加工は機械に加工させずに、作業者が加工をすることで効率が上がる場合があります。