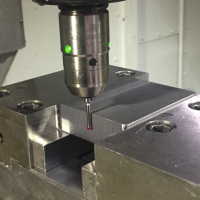
過去に加工実績のある場合は段取り表を見たり、NCプログラムから加工原点の位置を確認してワーク座標設定をしますが、新規などの加工は、加工に使う機械、材料、図面から自分で設定します。
今回はマシニングセンタでタッチセンサーとピックテスターを使って芯出しと加工原点の設定を紹介します。
バイスに角材料を取り付けた加工
バイスを使って図面のような四角い材料の加工をする場合
図面通りの向きでバイスに取り付けて加工します。
Y軸
材料を取り付けるバイスの面が機械の動きに対して平行に出ているか確認します。
バイスの通りだし作業はコチラで紹介しています。
バイスの平行の確認ができたらタッチセンサーに交換をして
バイスにタッチセンサーを当てて相対を0にセットします。
相対を0にセットしたら一旦バイスからタッチセンサーを離してタッチセンサーの向きを180度回転させて
180度回転した位置でもう一度バイスにタッチセンサーを当てて相対を確認します。
ずれている数値の半分の位置(-0.01なので-0.005)が加工原点になります。
相対座標-0.005の位置でワーク座標設定をします。
X軸
Y軸はバイスの口金で平行の確認をして0が出ていたので、バイスのどの面にタッチセンサーを当てて加工原点の設定をしても問題ありませんでしたが、
取り付けた材料の直角が出ていない場合、タッチセンサーの当てる位置を考える必要があります。
(0.1mmずれている状態)
画像のようにバイスの口金に近い位置を加工原点にして加工をした場合、
奥から5.0mm・5.05mm・5.1mmという傾向になります。
画像のようにバイスの口金から少し離れた位置を加工原点にして加工をした場合、
奥から4.95mm・5.0mm・5.05mmという傾向になります。
画像のようにバイスの口金の反対側を加工原点にして加工をした場合、
奥から4.9mm・4.95mm・5.0mmという傾向になります。
側面に削り代がある場合、段取りを変えて側面を削って成形する加工を増やします。
(わざと少し削り残して直角が出ていなかった証拠を残して加工する場合があります)
Z軸
X軸と同じく、材料がどのように取りついているか確認します。
図面と加工内容からどの程度加工面がずれていていいのか判断し、タッチセンサーを当てて加工原点に設定します。
平面が出ていない場合の原因は
- 機械に取り付けたバイスの平面が出ていない
- バイスの上に乗せた敷板が出ていない
- 材料に歪み、厚みにばらつきがある
- バイスで押さえる力で変形、動いている
など考えられます。
加工原点にタッチセンサーを当てることができない場合
画像のように加工原点にタッチセンサーを当てることができない場合
一旦違う所で加工原点を取ります。
(加工原点設定なのである程度しっかりした場所)
加工に使うワーク座標系に設定します。
G54は加工に使うワーク座標系
G55は控えとして入力
ワーク座標設定が完了したらタッチセンサーをピックテスターに交換します。
ピックテスターと相対座標系を使ってタッチセンサーで設定した位置から
加工原点に設定したい位置までの距離を測定します。
タッチセンサーで設定した位置から
加工原点に設定したい位置までの距離が18.213なので、ワーク座標系に増分値入力します。
これでX軸の加工原点の設定ができました。
G54は加工物の側面
G55はバイスの側面(控えなので無くても良い)
G56はバイス側面から加工物側面までの距離(控えなので無くても良い)
になります。
円盤形状の芯出し
画像のような円盤形状の芯出し
両側から旋盤加工されている材料です。
材料の取り代が多い場合の芯出し
削りだしの加工で材料の取り代がある場合、その取り代内であれば、材料の中心と加工原点がずれてしまっても不良品にはなりません。
取り代が多い場合、芯出し作業の質を落とし簡単な作業にします。
材料は260mmx115mmx25mmです。
バイス側面にタッチセンサーを当てて相対座標を0にセットします。
(ハンドル操作は0.1のままで作業)
反対側のバイス側面にタッチセンサーを当てたときの相対座標を確認します。
この半分に移動した所がバイスの中心で、ここを加工原点に設定します。
材料の取り付けはバイスからはみ出した所が均等になるようにします。
取り代が5mmあるので時間や気を使わずにセットします。
材料が2枚あるので、わざと1mmずらして加工してみました。
左が正規の位置で加工、右が1mmずらした加工です。
底面の残り代の違いが確認できます。
機械の円中心点計測機能を使った芯出し
ワークオフセット画面にある円中心点計測機能を使って芯出しをします。
画像のようにタッチセンサーを当てて赤枠部の測定を押して入力します。
同じように3等配に近い位置で残り2ヶ所入力します。
3ヶ所入力すると黄枠部に中心位置が入力されるので、赤枠部の書き込みを押して座標入力をします。
今度は画像のように残り2ヶ所を近い位置でG55に入力してみます。
ほぼ同じ位置で芯出しが出来ています。
芯出しに使う円が出ていれば簡単に芯出しができます。
今回の材料のように溝がある場合、前工程の加工順序次第では内径溝付近に歪みがある場合があり、正しい芯出しができない可能性があります。
便利な機能ですが、テスターを主軸に取り付けて回して芯出しをするのと違い歪みなどの確認ができず、3点で芯出しをするので3点の位置が重要です。
円中心点計測機能を使う場合、タッチセンサーを当てる位置が芯出しに相応しい位置か検討してください。
最後に
芯出し、加工原点の設定作業自体は、そんなに難しくありません。
精度の高い製品になると機械上では0で出ていても検査機では出ていないなんて事はよくあり、
加工原点をずらして加工する場合もあります。
芯出し、加工原点の設定はどこで、どの方法で作業をするのかが重要です。
他にも紹介できる作業方法があるので端材が出たり、機械が空いた時に記事を追記していきます。